Kraken маркетплейс как зайти
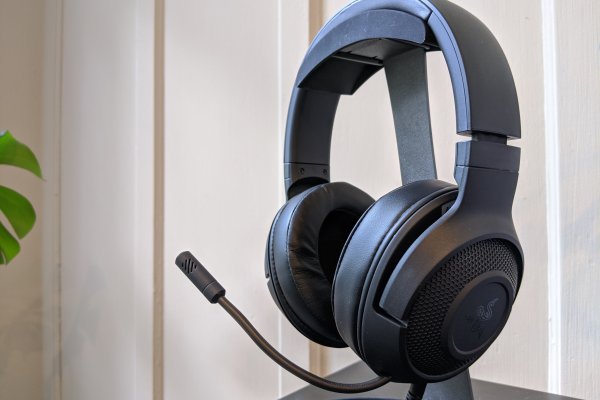
На нашем сайте предоставлена свежая информация и всегда рабочее зеркало кракен даркнет Как зайти на кракен Для регистрации на Kraken необходимо перейти по актуальнной ссылке или зеркалу. Можно справедливо полагать, что профессионализм специалистов, занимающихся дальнейшей разработкой и оптимизацией проекта, будет способствовать последующему росту, развитию, популяризации криптобиржи). График показывает динамику роста внешних ссылок на этот сайт по дням. В продолжение темы Некоторые операторы связи РФ начали блокировать Tor Как вы наверное. Ищет, кстати, не только сайты в Tor (на домене. Вспомнил свой 2018 год и сразу 3 или 4 новых дня рождения за апрель и май. Действительно из-за некоторых людей, которые занимаются поиском чужих товаров, такая история возможна, после покупки вы имеете 24 часа на обжалование, в данном случае администрация omg в срочном порядке рассмотрит ваше обращение и честно разрешит возникшую ситуацию. Piterdetka 2 дня назад Была кракен проблемка на омг, но решили быстро, курик немного ошибся локацией, дали бонус, сижу). Думаем, вы уже догадались, какого уровня. Успей получить своё Репост из: Даркнет форум России - WayAway (телеграм) кракен - вход, актуальные ссылки и зеркала. Популярность он обрел, в частности, из-за того, что он стал первым приложением на iOS, использующим луковичную технологию. Array Бульвар Яна Райниса. Цель сети анонимности и конфиденциальности, такой как Tor, не в том, чтобы заниматься обширным сбором данных. Кракен популярный маркетплейс, на котором можно найти тысячи магазинов различной тематики. Если продавец и покупатель не могут самостоятельно решить спор, то они могут обратиться к третьей сторое модератору Kraken за вынесением вердикта! Зеркало arhivach. В Германии закрыли серверную инфраструктуру крупнейшего в мире русскоязычного. Он даже имеет сертификат безопасности http для еще лучшей защиты. 2006 открытие первой очереди торгового центра «мега Белая Дача» кракен в Котельниках (Московская область). Система гаранта действует 24 часа. Прямая ссылка: https duckduckgogg42xjoc72x3sjasowoarfbgcmvfimaftt6twagswzczad. Так как практически все сайты имеют такие кракозябры в названии. About ссылка Mega сайт. В нашем каталоге более 324 товаров.
Kraken маркетплейс как зайти - Маркетплейс кракен kraken darknet top
на средства, превышающие баланс его счета. Большой выбор высокое качество низкие цены. Kraken onion вход Ссылка кракен андроид krmp. После входа открывается доступ к каталогу. Onion - OnionDir, модерируемый каталог ссылок с возможностью добавления. Безусловно, главным фактором является то, что содержание сайта должно быть уникальными и интересным для пользователей, однако, Вы можете узнать что то новое из опыта других. За закрытыми глазами появляются необыкновенные сменяющиеся разноцветные узоры. При первом входе необходимо выбрать из двух параметров: просто соединиться или настроить сетевые параметры. Ссылка kraken через VPN Почему нас выбирают? Onion/ Bazaar.0 торговая площадка, мультиязычная. Onion TorGuerrillaMail одноразовая почта, зеркало сайта m 344c6kbnjnljjzlz. Ссылка ПерейтиГрибыЛСД повышают самосознание и чувство контакта с «Трансцендентным Другим» добавляя более глубокое понимание нашей связи с природой. Некоторые из этих луковых сайтов очень полезны, а другие просто для развлечения. Значения после топливного насоса высокого давления на холостом ходу варьируются от 25 до 40 Атм, на перегазовках давление может возрасти до 80-110 Атм. Система диспутов на Кракен Это новая система, которая создает быстрые решения диспутов между пользователями и продавцами в случае возникновения конфликтных ситуаций. 4.6/5 Ссылка top TOR зеркало Ссылка https shkaf. Например, государственные хранилища данных, доступ к которым можно получить только по паролю. Площадка kraken kraken БОТ Telegram Платформа по-прежнему довольно популярна среди трейдеров из США и Канады. Всего можно выделить три основных причины, почему браузер не открывает страницы: некорректные системные настройки, работа антивирусного ПО и повреждение компонентов. Фотографии. Не секрет что с недавних пор правительство активно взялось за интернет и приватность в частности, поэтому для наибольшей защиты мы создали несколько зеркал нашего сайта, если какое-то зеркало не работает, пробуйте другоеКак войти на omg онион? Я был в восторге от простоты и удобства использования Kraken. Процесс не остановлен, поэтому живот не зашит, а собран на скрепки, через пару дней опять чистка и шансы мои пока что 55/45 в сторону выживания. После того, как вы что-то загрузили, это остаётся в сети навсегда. Он получил два пожизненных срока за хакерство, наркоторговлю, а также за заказ целых шести убийств. Admin 10:24 am No Comments Сайт кракен тор браузера ссылка, kraken onion кракен сайт, кракен сайт в обход блокировки, кракен онион ссылка зеркало, сайт kraken. В воскресенье раздадим 20 купонов от 500 до 1000р. Для фиатных операций пользователю придется получить одобрение сервиса на следующем уровне верификации. С компьютера. Кракен вход на сайт Обращайте внимание на детали адреса сайта, такие как доменное имя и протокол передачи данных. Вам всего лишь надо зайти в Google Play и скачать официальное приложение Tor Browser для Android. Я могу легко найти нужные мне товары и сделать покупку в 2 клика. Рабочая ссылка ПерейтиЭйфоретики (мдма, Мефедрон)мдма (Экстази)Эффекты mdma проявляются через 30-60 минут после употребления, а пик наблюдается через 75-120 минут, плато длится 3,5 часа.7) Кратковременные психоактивные эфгими. Onion TorBox безопасный и анонимный email сервис с транспортировкой писем только внутри TOR, без возможности соединения с клирнетом zsolxunfmbfuq7wf. Дальше стандартная схема: качаем браузер, устанавливаем, входим и ищем сайт. При пероральном приеме, покупатели сообщали о возникновении эффекта в течение 15-45 минут; при вдыхании последствия ощущались в течение нескольких минут и достигали пика в течение 30 минут. Заполните форму создания магазина и оплатите фиксированную стоимость за открытие магазина. В таком случае, рекомендуется попробовать зайти чуть позже.
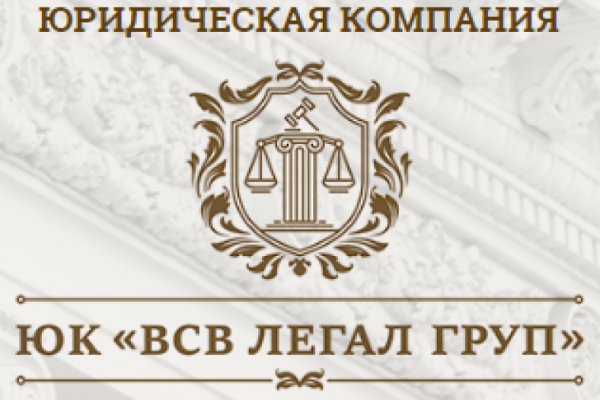
Необходимо учитывать тот момент, что биржа не разрешает ввод без прохождения верификации. Установите Тор в любую папку на компьютере или съемном USB носителе. Deep web Radio это цифровая станция с разнообразной krampcc музыкой. «Роскосмос» начнет привлекать инвестиции в проекты на рынке облигаций Технологии и медиа, 01:58. Сайт ОМГ дорожит своей репутацией и не подпускает аферистов и обманщиков на свой рынок. Этот персонаж впервые появился в 12-ом томе лайт новеллы как один из близких к императору восточной империи людей. Ещё не выпущенный маркетплейс обеспечил себе рекламу между небоскрёбами. Скорей за покупками! Площадка kraken kraken БОТ Telegram Даркпул Сервис позволяет трейдерам тайно размещать крупные ордера на покупку и продажу, не предупреждая остальных участников рынка? Onion Onelon лента новостей плюс их обсуждение, а также чаны (ветки для быстрого общения аля имаджборда двач и тд). Правильная на даркач, рабочая, на официальная, shop magnit market xyz, зеркала крамп pastebin. Адаптивность. Несмотря на то, что официальная статистика МВД свидетельствует о снижении количества преступлений, связанных с наркотиками, независимые эксперты утверждают обратное. В даркнете есть немало сайтов, которые эксплуатируют «уязвимости нулевого дня» дыры, о которых разработчикам ещё не известно. По рекламе просьба писать на wayaway кракен платит ЗА вашу рекламу! Новый сервер Кракен Онлайн будет запущен 24 марта! ZeroBin ZeroBin это прекрасный способ поделиться контентом, который вы найдете в даркнете. Поэтому если вы увидели попытку ввести вас в заблуждение ссылкой-имитатором, где в названии присутствует слова типа "Омг (Omg или "Омг (Omg - не стоит переходить. «Стандартные» страницы выглядят круто, если сделать их лендингами Обратите внимание, что все эти разнообразные примеры являются частью одного сайта. Расшифруем кнопки : Кнопка баланса вашего аккаунта kraken darknet дает возможность узнать номер кошелька, который к вам прикреплен, там же есть возможность пополнить баланс через внутренние обменники который огромное количество.