Как восстановить аккаунт на кракене
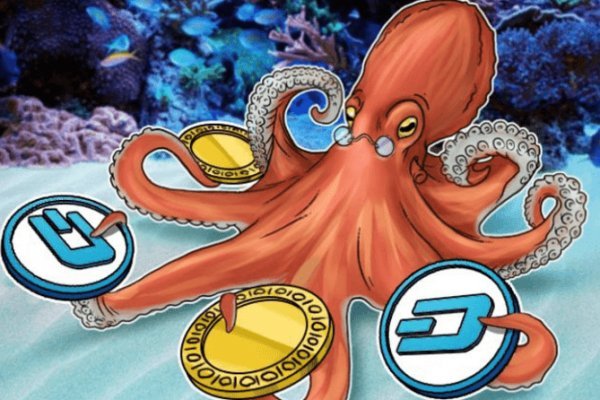
Как попасть на russian anonymous marketplace? Это попросту не возможно. Onion - одна из крупнейших площадок теневой торговли. На самом деле это сделать очень просто. После этого поиск выдаст необходимы результаты. Hiremew3tryzea3d.onion/ - HireMe Первый сайт для поиска работы в дипвебе. Фарту масти АУЕ! Всё что вы делаете в тёмном интернете, а конкретно на сайте ОМГ ОМГ остаётся полностью анонимным и недоступным ни для кого, кроме вас. Во-первых, в нём необходимо вручную выбирать VPN нужной страны. TJournal попробовал самые популярные средства обхода блокировок и нашёл среди них версии «для чайников» в которых всё работает сразу, без настроек. МВД РФ, заявило о закрытии площадки. Читайте также: Очистка мака от ненужных файлов. Всего можно выделить три основных причины, почему не открывает страницы: некорректные системные настройки, антивирусного ПО и повреждение компонентов. Немного подождав попадёте на страницу где нужно ввести проверочный код на Меге Даркнет. Даркмаркет направлен на работу в Российском рынке и рынках стран СНГ. Русское сообщество. Сервис от Rutor. Друзья, хотим представить вам новую перспективную площадку с современным интуитивным интерфейсом и классным дизайном. Главный минус TunnelBear цена. Org так и не открылись. Дизайн необходимо переработать, или навести порядок в существующем. Так как сети Тор часто не стабильны, а площадка Мега Даркмаркет является незаконной и она часто находится под атаками доброжелателей, естественно официальная маркетплейс может временами не работать. Вход Для входа на Мега нужно правильно ввести пару логин-пароль, а затем разгадать капчу. Заголовок ответа сервера http/1.1 200 OK Date: Thu, 08:06:39 GMT Server: Apache/2.2.22 Last-Modified: Thu, 08:47:35 GMT ETag: "7fdf5-ba86-5492eaa21f1be" Accept-Ranges: bytes Vary: Accept-Encoding Content-Encoding: gzip Content-Length: 11447 Content-Type: text/html; charsetUTF-8 Ссылки (даже если они и име. Показало себя заметно хуже. Вас приветствует обновленная и перспективная площадка всея русского даркнета. Onion - Скрытые Ответы задавай вопрос, получай ответ от других анонов. Как мы знаем "рынок не терпит пустоты" и в теневом интернет пространстве стали набирать популярность два других аналогичных сайта, которые уже существовали до закрытия Hydra. Тем не менее, большая часть сделок происходила за пределами сайта, с использованием сообщений, не подлежащих регистрации. Оригинальный сайт: ore (через TOR browser) / (через Тор) / (онион браузер).Сборник настоящих, рабочих ссылок на сайт мега в Даркнете, чтобы вы через правильное, рабочее зеркало попали на официальный сайт Меги. Ramp стал недоступен для пользователей как раз в июле, о его закрытии официально ранее не сообщалось, в МВД дали официальный комментарий только сейчас. Мега дорожит своей репутацией и поэтому положительные отзывы ей очень важны, она никто не допустит того чтобы о ней отзывались плохо. Onion - the Darkest Reaches of the Internet Ээээ. Требует включенный JavaScript. Чаще всего они требуют всего лишь скопировать ссылку в строку на своей главной странице и сделать один клик. Как использовать. Окончательно портит общее впечатление команда сайта, которая пишет объявления всеми цветами радуги, что Вы кстати можете прекрасно заметить по скриншоту шапки сайта в начале материала. Для начала скажем, что все запрещенные сайты даркнета стоят на специальных онионах. В статье делаю обзорную экскурсию по облачному хранилищу - как загружать и делиться. Mega darknet market и OMG! Часто сайт маркетплейса заблокирован в РФ или даже в СНГ, поэтому используют обходные зеркала для входа, которые есть на нашем сайте. Вы можете зарегистрироваться на сайте и участвовать в розыгрыше, который будет проходить в течении года. Можно добавлять свои или чужие onion-сайты, полностью анонимное обсуждение, без регистрации, javascript не нужен. Onion - Daniel Winzen хороший e-mail сервис в зоне.onion, плюс xmpp-сервер, плюс каталог онион-сайтиков. Onion - Verified зеркало кардинг-форума в торе, регистрация.
Как восстановить аккаунт на кракене - Vk8 at кракен рабочий
�нской сцене 1990-х годов 225 226. Запустить диспут необходимо до того, как сделка будет закрыта. Для данной платформы невозможно. Впрочем, если блицкриг против RuTor не удастся, владельцы форума и маркетплейса OMG могут подкопить средства и дать серьезный отпор элите даркнета с «Гидры». Но поменялся производитель, я даже не вспомню названия этого препарата. Television overview by Mike McGuirk (англ.). Они пытаются вычислить операторов и администраторов ресурса, чтобы предъявить им обвинения в распространении наркотиков и отмывании денег. Это было абсолютно бесплатно, абсолютно доступно. Сайт пользуется особой популярностью в даркнете, где предлагаются к покупке запрещенные вещества, препараты, а также есть услуги программистов по взлому аккаунтов, почты. В якийсь момент ти починаєш виносити речі з дому, і зрештою твоя. Откройте нужную страницу, изображение или документ. Нужны выбрать рабочее зеркало ОМГ. Так проверяются даже услуги на официальном сайте омг даркнета. Карточки Изъятие наркотиков должно проводиться либо в присутствии двоих понятых, либо с использованием технических средств фото- или видеофиксации. 51 Конституции. После того, как вы выберете изображение, которое хотите загрузить, нажмите на предварительный просмотр изображения. Самой надёжной связкой является использование VPN и Тор. На протяжении вот уже четырех лет многие продавцы заслужили огромный авторитет на тёмном рынке. Требуется помощь? Ряд экспертов полагает, что группа спасла британскую рок-музыку и определила форму и звучание лучших коллективов 1990-х 92 Помимо Happy Mondays и The Stone Roses, новое направление объединило группы со схожим звучанием, такие как The Charlatans и Inspiral Carpets комм. Такая вот история была у меня, печальная. Расскажи, для начала, о себе. Но впоследствии участие защитника, просто подписавшего необходимые документы и молчавшего на протяжении всех следственных действий, будет признано достаточной и квалифицированной юридической помощью. The Manics' lyrics were something special (англ.). Какие заболевания есть в твоем анамнезе? Как отправить фото в диспуте на гидре! В организации поясняют, что такой наркотик из аптеки особенно опасен. В любом случае, хоть RuTor и вызывает ностальгические чувства у многих обитателей закрытой части интернета, и ему есть альтернатива. Допустим, товар стоит 10 000, а на балансе всего 3 000. Говорят, что люди хотят узнать, как попасть в даркнет, по таким трем причинам: Если вам нужен криптокошелек для Даркнета, то Rahakott подойдет как нельзя лучше. Прямой катетер поставили и переливали, только это спасло меня, потому что было ужасное состояние. З охочими купити наркотик зловмисники спілкуються зазвичай у Telegram. Врач мне протягивал таблетки, а я очень боялась их пить. Спасибо, Юля.

HomeWho WeAreAboutAlcazar EnergyOur TeamCorporate & Investment ManagementDelivery& OperationsBusinessSupportSustainabilityOur Sustainability PrinciplesParticipant to the United Nations Global Compact (UNGC)OurInvestmentsAboutAEP-IRealisedInvestmentsMediaNewsVideosContact UsInvestor AreaAlcazar Energy exited the largest independent portfolio ofrenewable energy in the MENA regionGenerated over 4,200 jobs during the construction of AEP-Iassets, of which 80% were in-country445,000+ tons of CO₂ emissions avoided per year through theoperation of AEP-I assetsAbout Alcazar EnergyAlcazar Energy is an independent fund managementcompany focused on investing, financing, and developingutility scale renewable energy capacity in selected emergingmarkets.read moreSustainabilityread moreOur Teamread moreOurInvestmentsread moreWho We AreAboutAlcazar EnergyOur TeamOurInvestment PropositionSustainabilityOur PrinciplesOurInvestmentsAboutAEP1RealisedInvestmentsMediaNewsVideosContact |Terms