Сайт кракен не работает почему
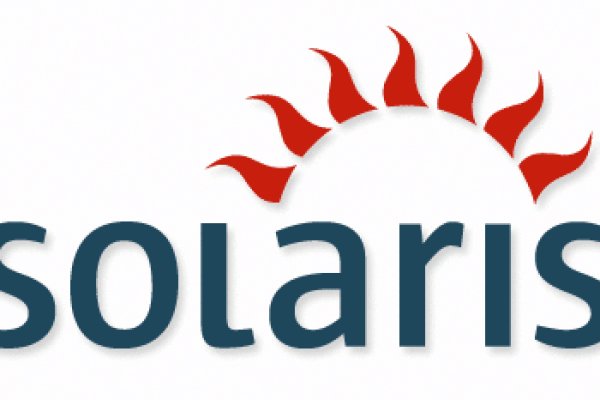
Onion/ - 1-я Международнуя Биржа Информации Покупка и продажа различной информации за биткоины. Постараюсь объяснить более обширно. Особых знаний для входа на сайт Мега не нужно - достаточно просто открыть браузер, вставить в адресную строку Мега ссылку, представленную выше, и перейти на сайт. Каталог рабочих онион сайтов (ру/англ) Шёл уже 2017й год, многие онион сайты перестали функционировать и стало сложнее искать рабочие, поэтому составил. Топчик зарубежного дарквеба. Введя капчу, вы сразу же попадете на портал. Не можете войти на сайт мега? Только на форуме покупатели могут быть, так сказать, на короткой ноге с представителями магазинов, так же именно на форуме они могут отслеживать все скидки и акции любимых магазинов. Просмотр. Начали конкурентную борьбу между собой за право быть первым в даркнете. Есть закрытые площадки типа russian anonymous marketplace, но на данный момент ramp russian anonymous marketplace уже более 3 месяцев не доступна из за ддос атак. Всем мир! Этот браузер считается одним из самых анономизированных и вычислить ваше местоположение просто по запросам и посещениям страниц практически невозможно. Всё, что надо знать новичку. Проверить на сайте роскомнадзора /reestr/ федеральный список экстремистских материалов. Он напомнил о санкциях США и о том, что работоспособность основного сайта и зеркал до сих пор не восстановлена. Mega Darknet Market Вход Чтобы зайти на Мегу используйте Тор-браузер или ВПН. Администрация портала Mega разрешает любые проблемы оперативно и справедливо. Основателем форума являлся пользователь под псевдонимом Darkside. Например, легендарный браузер Tor, не так давно появившийся в сериале «Карточный домик» в качестве средства для контакта с «тёмным интернетом без проблем преодолевает любые блокировки. Встроенный в Opera сервис VPN (нажмите). Zerobinqmdqd236y.onion - ZeroBin безопасный pastebin с шифрованием, требует javascript, к сожалению pastagdsp33j7aoq. Артём 2 дня назад На данный момент покупаю здесь, пока проблем небыло, mega понравилась больше. Спасибо администрации Mega Onion и удачи в продвижении! Официальные ссылки на Мегу Пользователям портала Мега зеркало рекомендуется сохранить в закладки или скопировать адрес, чтобы иметь неограниченный доступ к порталу. Onion - Dark Wiki, каталог onion ссылок с обсуждениями кракен и без цензуры m - Dark Wiki, каталог onion ссылок с обсуждениями и без цензуры (зеркало) p/Main_Page - The Hidden Wiki, старейший каталог.onion-ресурсов, рассадник мошеннических ссылок. На нашем сайте представлена различная информация о сайте.ru, собранная из открытых источников, которая может быть полезна при анализе и исследовании сайта. Они не смогут скрываться в даркнете или на форумах, они не смогут скрываться в России или где-то в других странах сказано в заявлении Минфина. Mixermikevpntu2o.onion - MixerMoney bitcoin миксер.0, получите чистые монеты с бирж Китая, ЕС, США. К сожалению, требует включенный JavaScript. Оплата картой или криптой. Telefon oder E-Mail Passwort Забирай! Однако скорость его работы заставляет вспомнить о временах модемов, подключающихся к сети через телефонную линию. Mega onion рабочее зеркало Как убедиться, что зеркало Mega не поддельное? И предварительно, перед осуществлением сделки можно прочесть. Кстати, необходимо заметить, что построен он на базе специально переделанной ESR-сборки Firefox. Ни блог Навального, ни трекер Rutor. Рядом со строкой поиска вы можете найти отзывы о товаре, который искали, а так же рейтинг магазина, который выставляют пользователи, которые уже закупались, а так же там показаны некоторые условия товара, если они имеются. "С зеркало 27 июля по года сотрудники гунк МВД России совместно с УНК Москвы, Московской области, Санкт-Петербурга и Ленинградской области разоблачили и пресекли деятельность межрегиональной орем. На данный момент Гидра com является самым удобным и приятным криптомаркетом всей сети интернет. Изредка по отношению к некоторым вещам это желание вполне оправдано и справедливо, однако чаще всего - нет. Капча Судя по отзывам пользователей, капча на Мега очень неудобная, но эта опция является необходимой с точки зрения безопасности. Он годится как закрытый инструмент, не влияющий на работу остальной системы. Так как система блокчейн имеет свои особенности, стоит это учитывать перед тем как пополнить баланс на Мега Даркнет. Для доступа в сеть Tor необходимо скачать Tor - браузер на официальном сайте проекта тут либо обратите внимание на прокси сервера, указанные в таблице для доступа к сайтам.onion без Tor - браузера. Diasporaaqmjixh5.onion - Зеркало пода JoinDiaspora Зеркало крупнейшего пода распределенной соцсети diaspora в сети tor fncuwbiisyh6ak3i.onion - Keybase чат Чат kyebase. Ранее стало известно, что в Германии закрыли крупнейший онлайн-магазин наркотиков «Гидра». И постоянно предпринимают всевозможные попытки изменить ситуацию. Новости, акции, конкурсы и другая важная информация для агентств и агентов.
Сайт кракен не работает почему - Кракен ссылка тор браузер
Рабочие зеркала позволяют зайти на сайт omg onion через обычный браузер в обход запрета.ОМГ онион сайтДаркнет маркет ОМГВход на ГидруОМГ википедияОМГ онион ссылка на моментальные магазины в торЗакладки с веществами повсюду, в телеге, в торе, в центр веб.Спам который вы очень ждали: марихуана, марихуана, лсд, герыч, мефедрон, лсд — все в продаже на официальном сайте площадки омг.омг мусорскаяomg wiki ссылкакак зайти на omg со смартфонаomg кладкакая ссылка на гидру?омг не работаетшишки бошки омг гашишсоздатель omgомг нарко этосоздатель omgадмин гидрыне заходит на гидруомг бошкиМосква, Керчь, Воронеж, Казань, Челябинск, Омск, Минск, Кострома, Астана, Астана, Кемерово, Хабаровск, Пермь, вся Страна.Площадка omg ОМГ — криптомаркет нового поколения.ОМГ ТORговая площадкаСсылки omgomg Onion (магазин ОМГ онион) — уникальная торговая площадка в сети ТОР.
Криптомаркет продает по всей территории РФ, Беларусии, Украины, Казахстана функционирует круглосуточно, 7 дней в неделю, круглосуточная онлайн-поддержка, гарант, автоматизированные продажи с опалтой через киви или bitcoin.
omg полностью безопасна и написана на современных языках программирования.
Основная проблема при регистрации на гидре – это поиск правильной ссылки. Помимо тор ссылки, есть ссылка на гидру без тора.Преимущества сайта криптомаркета заключаются в том, что:ОМГ — самый простой и безопасный криптомаркет для покупки товара;Интернет-магазин лучший в РФ, СНГ и за границей. Есть несущественных отличий, в сравнении с другими площадками, благодаря которым покупатели и продавцы всегда выбирают только Гидру;Отсутствует общеизвестные уязвимости в кибербезопасности (по заявлению администрации omg центр);Вы можете завести собственный биткоин-кошелек, через обменник биткоина (киви в биткоин);Сайт обладает лучшей системой анонимности. За все время работы площадки не было утечек личных данных пользователей сайта.Постоянно возникают новые инструменты, позволяющие действовать в сети анонимно.
В следствии чего возникли onion сайты (порталы, существующие в доменной зоне onion).Из полезных фич:не нужно ждать подтверждения транзакции в блокчейне;не нужно ждать подтверждения транзакции в блокчейне;не нужно ждать подтверждения транзакции в блокчейне;пополнить баланс теперь можно даже через Сбербанк.пополнить баланс теперь можно даже через Сбербанк.не нужно ждать подтверждения транзакции в блокчейне;Для перемешивания лайткоинов используйте блендер биткоиновbitcoin mixerКак уже было отмечено, площадка ОМГ – самый крупный центр торговли в тор браузере.
В данном маркетплейсе есть возможность приобрести то, что в открытом доступе купить критически сложно или невозможно вообще. Каждый зарегистрированный покупатель может зайти в любой из имеющихся на сервисе магазинов и купить нелегальный товар, организовав его поставку в города России и страны СНГ. Покупка возможна в любое время суток из любого региона. Особое преимущество данной площадки это систематическое и регулярное обновление ассортимента магазинов.Выбрать и купить товар услугу не составит труда. Перед покупкой можно ознакомиться с отзывами предыдущих покупателей.
Поэтому посетитель сайта может заблаговременно оценить качество покупки и решить, нужен ему товар или все же от покупки стоит отказаться.Приемущество анонимного интернет-криптомаркета в наличии службы тайных покупателей. Они следят за тем, чтобы товары, которые представлены в магазинах соответствовали определенным требованиям и даже делают в частных случаях химический анализ предлагаемых веществ. Если по каким-то причинам всплывает несоответствие качеству товара, товар немедленно снимают с продажи, магазин блокируют, продавец блокируется.Доставку вещества можно заказать в любой регион Страны и СНГ, указав координаты, где будет удобно забрать прикоп. Покупка отдается в виде закладки. Только после того, как покупатель подтвердит наход товара, удостоверится в качестве продукта продавец получает свои деньги. Если с качеством или доставкой в результате покупки возникли проблемы, клиент имеет право инициировать спор, к которому сразу подключатся независимые администраторы Гидры.Оплата реагентов производится в биткоинах, и в большинстве случаев продавцы предпочитают принимать оплату через внутренний счет магазина. Однако некоторые маркеты готовы принять оплату рублями через QIWI-кошелек. Сами админы портала советуют производить оплату биткоинами, так как это самый надежный способ оплаты, который также позволяет сохранить анонимность проводимых сделок.Что такое Тор браузер и зачем он нуженTOR — это военная технология, которая позволяет скрыть личность пользователя в сети интернет. Расшифровывается TOR как The Onion Router — луковый маршрутизатор.
Тор изначально был военным проектом США, но в скором времени его открыли для спонсоров, и теперь он называется Tor Project. Основная идея этой технологии — обеспечение анонимности и безопасности в сети, где большинство участников не верят друг другу. Смысл этой частной сети в том, что трафик проходит через несколько компьютеров, шифруются, у них меняется IP и вы получаете зашифрованный канал передачи данных.Что точно необходимо учитывать при работе с Гидрой?От некачественных сделок с моментальными магазинами при посещении портала не застрахован ни один пользователь.В связи с этим модераторы портала рекомендуют:смотреть на отзывы.
Отзывы покупателей это важнейший критерий покупки. Отзывы могут повлиять на окончательное решение о покупке товара или клада. Благодаря оставленным комментариям можно узнать о качестве товара, способах его доставки и других деталях сотрудничества с магазином;подтверждать покупку только после того, как будет подтверждено ее качество. Если появились проблемы, а подтверждение уже сделано, в таком случае средства не удастся вернуть;обязательно оставлять отзывы после покупки. Это поможет другим покупателям сделать правильный выбор и не ошибиться при покупке;придумывать только новые пароли и логины для каждого пользователь перед регистрацией. Желательно, чтобы пароли и логины, не были ранее задействованные на других ресурсах. Это позволит соблюсти анонимность;Обратите внимание, что переодически домен Гидры обновляется ее программистами. Дело в том, что сайт практически ежедневно блочат, и пользователю в результате не удается зайти на площадку, не зная рабочих ссылок. Чтобы избежать эту проблему, сотрудники портала рекомендуют добавить официальную страницу Гидры в закладки. Сохрани все ссылки себе на сайт и делись ими со своими друзьями.Потенциальный пользователь должен пройти регистрацию для того, чтобы пользоваться всеми возможностями Гидры.Когда модератор подтвердит регистрацию продавца, он получит доступ к правилам пользования площадки. Также сразу после входа он получит возможность пополнить баланс аккаунта, чтобы тут же приступить к покупкам.Пополнение баланса на Гидре заслуживает отдельного внимания. Дело в том, что для внесения в кошелек стандартной валюты площадки – BTC – требуется сначала купить фиат, который сразу нужно будет обменять на криптовалюту. Купить его можно либо на криптовалютной бирже, либо в встроенном пункте обмена.Когда фиат будет куплен и обменен на определенное количество биткоинов, останется перевести деньги в системе. Чтобы это сделать, нужно скопировать адрес биткоин кошелька, который был выдан при регистрации, и отправить на него нужную сумму с помощью использования различных платежных систем (например, QIWI). Также обмен на биткоин может быть реализован на самой площадке магазина в специальном разделе «обмен».Как не попасть на сайт мошенниковДля защиты от мошеннических сайтов, была придумана сеть бесперебойных зеркал.Чтобы не попасть на мошеннические сайты сохраните ссылку зеркала на этот сайт в закладки. Скопируйте все ссылки с этого сайта к себе на компьютер так как Роскомнадзор может заблокировать сайт.
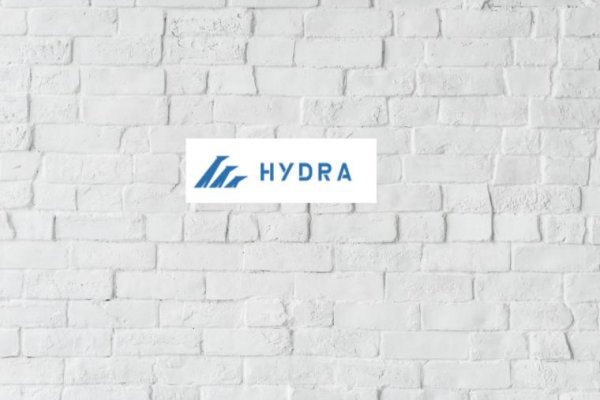
Onion - CryptoParty еще один безопасный jabber сервер в торчике Борды/Чаны Борды/Чаны nullchan7msxi257.onion - Нульчан Это блять Нульчан! Onion - cryptex note сервис одноразовых записок, уничтожаются после просмотра. При обмене киви на битки требует подтверждение номера телефона (вам позвонит робот а это не секурно! Торрент трекеры, библиотеки, архивы. Onion - Torrents-NN, торрент-трекер, требует регистрацию. Foggeddriztrcar2.onion - Bitcoin Fog микс-сервис для очистки биткоинов, наиболее старый и проверенный, хотя кое-где попадаются отзывы, что это скам и очищенные биткоины так и не при приходят их владельцам. Скачать можно по ссылке /downloads/Sitetor. Onion - Bitcoin Blender очередной биткоин-миксер, который перетасует ваши битки и никто не узнает, кто же отправил их вам. Иногда отключается на несколько часов. Регистрация по инвайтам. Org,.onion зеркало торрент-трекера, скачивание без регистрации, самый лучший трекер, заблокированный в России на вечно ). Раньше была Финской, теперь международная. Org в луковой сети. Зеркало сайта z pekarmarkfovqvlm. Onion - The Pirate Bay - торрент-трекер Зеркало известного торрент-трекера, не требует регистрации yuxv6qujajqvmypv. Playboyb2af45y45.onion - ничего общего с журнало м playboy journa. Onion/ - Форум дубликатов зеркало форума 24xbtc424rgg5zah. Требует включенный JavaScript. Hiremew3tryzea3d.onion/ - HireMe Первый сайт для поиска работы в дипвебе. Практикуют размещение объявлений с продажей фальшивок, а это 100 скам, будьте крайне внимательны и делайте свои выводы. Onion - Facebook, та самая социальная сеть.