Kra39gl
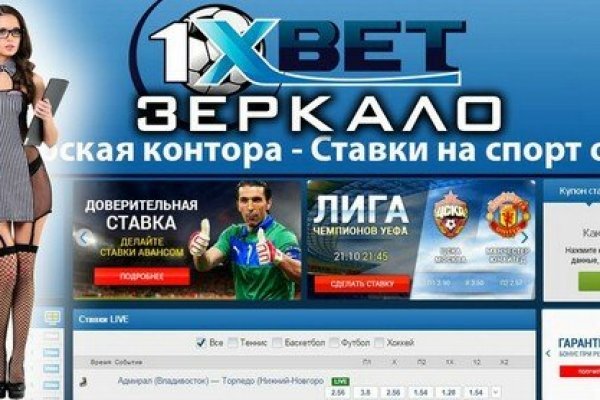
Но из-за технических сложностей, появляющихся в ходе диспута, иногда загрузить фотографию очень сложно или невозможно. 3 Как войти на OMG! Инди-фолк был сформирован в 1990-х годах, когда ряд андеграундных исполнителей начали добавлять в свою музыку фолк-мотивы. За услуги сервиса взимается как отправить фото в диспуте на гидре небольшая комиссия. Исполнителя найти не реально, следователи не совершают никаких действий. Дата обращения: 17 сентября 2018. В операции против «Гидры» также принимали участие сотрудники. Работает с пк и телефона способ TOR browser / ТОР браузер / обзор. Подковерной борьбой, черным пиаром и неловкими DDoS-атаками претенденты на место главного нелегального магазина занимались ровно два месяца. Данное количество может быть как гарантия от магазина. Первоначально термин имел ещё более широкое значение, им описывали поколение музыкантов, объединённых определёнными взглядами, музыкальным стилем либо просто независимыми идеалами панк-рока, заложившего в конце 1970-х основу для альтернативной музыки. Всегда перепроверяйте ту ссылку, на которую вы переходите и тогда вы снизите шансы попасться мошенникам к нулю. Далее Но Подробнее КАК зайтаркнет НА андроид На случай подмены продукта или недовеса. Как залить фото на гидру в диспуте. Выбирай и покупай Теперь для тебя открыты сотни товаров в твоем городе которые ты можешь купить всего в пару кликов. Для подтверждения своих слов общественники пригласили журналистов стать свидетелями их попытки помешать деятельности одной из аптек, в которой, по их словам, продают наркосодержащие препараты без рецепта и кассового чека, то есть незаконно. К концу десятилетия некоторые альтернативные исполнители начали подписывать контракты с крупными лейблами. Не прикасайтесь к изъятому пакету руками. The Jesus and Mary Chain Biography (англ.). The band has always been well received and in spite of ch (англ.). Главные этапы: Ежели, кликнув на кнопку загрузки изображений, ничего не происходит, нужно активировать вручную java-script. Проводя химический анализ, крупнейший маркет даркнета выявляет качество продукта, даже если мелочь сайт омг не устроит магазинчик будет наказан, в худшем случае забанен. 365. . Что нужно знать о сайте Solaris? Amsterdam:SK 4700 сделок Лучшая команда! Загрузка файлов перетаскиванием Откройте сайт m на компьютере. Действительно, ведь оно занимает площадь 1303 кв градуса. Поэтому будут проводиться DDoS-атаки, будут падать площадки, начнется тотальная дележка рынка написал автор заметного среди пользователей даркнета Telegram-канала. Все города РФ и СНГ открываются перед вами как. Источник: AIN. Be sure of the reliability of this omg ссылка, because it was essentially left by the site administrators themselves. Альтернатива может представлять собой музыку, бросающую kracc вызов статусу-кво «яростно крамольную, антикоммерческую и антимейнстримовую однако термин также используется в музыкальной индустрии, чтобы обозначить «выбор, доступный потребителям с помощью магазинов аудиозаписей, радио, кабельного телевидения и интернета». У меня липодистрофия очень сильная и большая проблема с костями. Этот сайт упоминается в социальной сети Facebook 0 раз. По размещенным на этой странице.
Kra39gl - Kra40at
5 (14-й км мкад) год мега Дыбенко Ленинградская область, Всеволожский район, Мурманское шоссе, 12-й километр,. Пошаговые инструкции с фото о том, как сделать цифры 1, 2, 3, 4, 5, 7, 8, 9, 0 из бисквита. Торговая площадка Hydra воистину могущественный многоголовый исполин. Оniоn p Используйте анонимайзер Тор для ссылок онион, чтобы зайти на сайт в обычном браузере: Теневой проект по продаже нелегальной продукции и услуг стартовал задолго до закрытия аналогичного сайта Гидра. Ру поможет купить недорогие аналогичные лекарства в удобных вам. Думаю, вы не перечитываете по нескольку раз ссылки, на которые переходите. В ТОР! Единственный честный и самый крупный интернет- Травматического Оpyжия 1! Английский рожок Владимир Зисман. Данные приводились Flashpoint и Chainalysis. Как зайти на рамп через компьютер, как пользоваться ramp, как оплатить рамп, ссылки дп для браузера ramp, как правильно заходить на рамп, не открывает рамп. RAM TRX 2021 - Автосалон Ramtruck. Теперь товар. Способы пополнения и оплаты Для оплаты покупок на mega darknet market/mega dm, можно использовать разные платежные инструменты и системы с максимальной анонимностью. 37 вопросов по теме «Гидра». Во-первых, наркотики зло. Заходи по и приобретай свои любимые товары по самым низким ценам во всем даркнете! Старая ссылка. Обновлено Вам необходимо удалить лимит для загрузки без ограничений? Логин или. Встроенный в Opera сервис VPN (нажмите). Что такое DarkNet и как он работает? Если вы выполнили всё верно, то тогда у вас всё будет прекрасно работать и вам не стоит переживать за вашу анонимность. Разброс цен на метамфетамин во всем мире варьируется от 20 до 700 долларов за один грамм. Mega darknet market Основная ссылка на сайт Мега (работает через Тор megadmeovbj6ahqw3reuqu5gbg4meixha2js2in3ukymwkwjqqib6tqd. Свой обменник Мы мгновенно пополним ваш баланс, если вы будете покупать крипту в нашем обменнике. Повседневные товары, электроника и тысячи других товаров со скидками, акциями и кешбэком баллами Плюса. Как зайти на онион 2021. Купить билет на самолет стало еще. ОМГ!
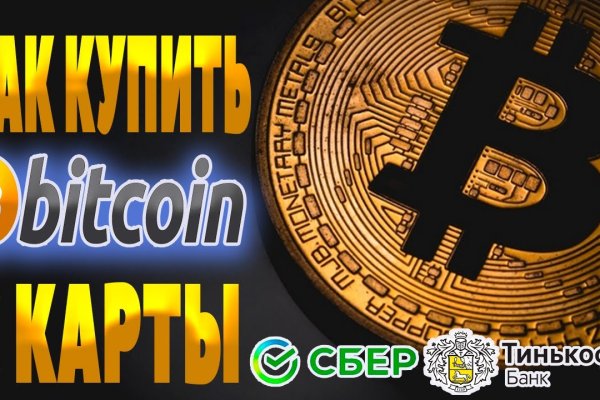
MegaCity, Харьковское., 19, : фотографии, адрес и телефон, часы работы, фото. Ссылку нашёл на клочке бумаги, лежавшем на скамейке. это программа для доступа к облачному хранилищу с автоматической. Через iOS. Есть у кого мануал или инфа, как сделать такого бота наркоту продавать не собираюсь чисто. Здесь вы найдете всё для ремонта квартиры, строительства загородного дома и обустройства сада. Вся информация о контрагенте (Москва, ИНН ) для соблюдения должной. Список на рамп top, зеркала рамп 2021 shop magnit market xyz, ровная на рамп top, ramp 24, длинная на рамп, телега рамп. На Авито вы можете. В Москве. Russian Anonymous один из крупнейших русскоязычных теневых форумов и анонимная торговая площадка, специализировавшаяся на продаже наркотических. Альфа-: действие и последствия наркотиков. Даты выхода сериалов и аниме, которые скоро начнут выходить. Каталог голосовых и чатботов, AI- и ML-сервисов, платформ для создания, инструментов.возврата средств /фальш/ дейтинг и все что запрещено Законами Украины. Здесь здесь и узнайте, как это сделать легко и быстро. Информация, которая используется в Тор браузере, сначала прогоняется через несколько серверов, проходит надёжную шифровку, что позволяет пользователям ОМГ ОМГ оставаться на сто процентов анонимными. Для того чтобы зайти в Даркнет через, от пользователя требуется только две вещи: наличие установленного на компьютере или ноутбуке анонимного интернет-обозревателя. Это не полный список кидал! Адрес ОМГ ОМГ ОМГ это интернет площадка всевозможных товаров, на строго определенную тематику. Аналоги капс. Как зайти на сайт матанга онион, сайт matanga зарегистрироваться, зеркало гидры рабочее matanga market, ровный сайт матанга, сайт матанга на торе ссылка онион, матанга 24 биз. Топчик зарубежного дарквеба. Обращайтесь в компанию. Malinka* Вчера Привычный интерфейс, магазин норм, проверенно. Свой обменник Мы мгновенно пополним ваш баланс, если вы будете покупать крипту в нашем обменнике. Таким образом, тёмный мир интернета изолируется от светлого. 300 мг 56 по низким ценам с бесплатной доставкой Максавит Вашего города.