Kra13.at
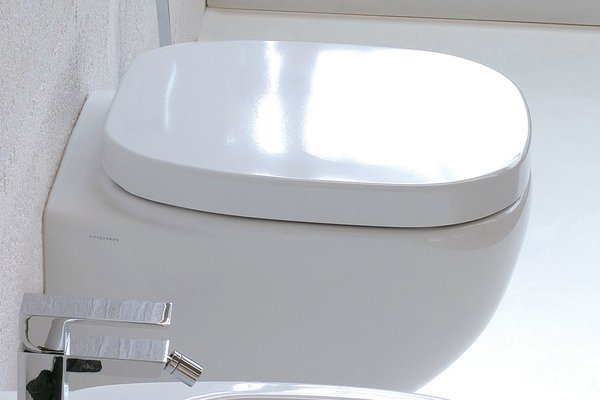
Hydra или «Гидра» крупнейший российский даркнет-рынок по торговле наркотиками, крупнейший в мире ресурс по объёму нелегальных операций с криптовалютой. Это означает, что каждые 2-3 дня она делает свою копию. Последние являются частью эктодермальных клеток колонны, особенно щупалец, где они упакованы в высокой плотности. В., Хабибулин. Сама «Гидра» в меморандуме конца 2019 года заявила о рекламном характере проекта. Эти маленькие вредители способны убивать и есть мальков рыбы и мелких взрослых рыб. 1 2 Кеффер, Лаура. По мнению президента Фонда имени Андрея Рылькова Анны Саранг, продолжительная и успешная, в сравнении с иностранными даркнет-рынками, работа «Гидры» обусловлена тем, что российские ведомства больше заинтересованы в создании видимости борьбы с наркоторговлей путём ареста её мелких членов. Если она достаточно мала, гидра ее съест. Г. Водоросли, живущие в пресноводной гидре, получают выгоду от защищенной безопасной среды и получают пищевые побочные продукты из гидры. Интересный факт: Пресноводная гидра не проявляет каких-либо признаков старения и выглядит бессмертной. Кроме наркотиков, популярными товарами на «Гидре» являлись фальшивые деньги и документы, инструкции по противозаконной деятельности. Гидры перемещают свои тела в воде, пока они прикреплены, расширяясь и сжимаясь под действием смеси мышечных движений и водяного (гидравлического) давления. Интересный факт: Примечательно, что даже клетки из механически отделенной пресноводной гидры могут восстановиться и в течение примерно недели вновь собраться в работающее животное. Они затеняют все стороны аквариума, кроме одной, и помещают стекло изнутри этой стены. Дата обращения: Архивировано года. Два вида, однако, являются отличительными. Все, что им нужно сделать, это освободить свою ногу и плавать в новом месте, или медленно продвинуться вперед, присоединяя и освобождая свои щупальца и ступню поочередно. Оniоn p Используйте анонимайзер Тор для ссылок онион, сайт чтобы зайти на сайт в обычном браузере: Теневой проект по продаже нелегальной продукции и услуг стартовал задолго до закрытия аналогичного сайта Гидра. Аналогичным образом, фертильность оставалась постоянной для 80 особей гидр со временем.
Kra13.at - Кракен продажа
крешении форума, сотрудники которого стояли у истоков самой «Гидры». Получить ссылку на Мега (Mega) и безопасно совершить покупку возможно на нашем сайте. Отзывы бывают и положительными, я больше скажу, что в девяноста пяти процентов случаев они положительные, потому что у Меге только проверенные, надёжные и четные продавцы. Далее рабочие зеркала на гидру я прилагаю правило о подмене товара (пункт правил.6) и прошу вернуть деньги. В мобильном приложении. Administration omgomg So far, little can be said about the omg сайт, but the site administration shows that they are constantly and painstakingly working to improve the quality of the site and its other components. Получается, из-за того, что я долгое время кололась в пах, когда межсезонье у меня опухают ноги. Со стороны правоохранительных органов. Она застывает, смотрит на мое «причинное место застыв, просто застывшая. Несмотря на то, что на Гидре работают честные продавцы, время от времени с кладом возникают недоразумения. Богатый функционал Самописный движок сайта (нет уязвимостей) Система автогаранта Обработка заказа за секунды Безлимитный объем заказа в режиме предзаказа. В суд подобные случаи почти не доходят, а местные жители очень неорганизованные, чтобы контролировать ситуацию (хотя сделать это могут только они отмечают в организации. Вход Как зайти на OMG! Можно воспользоваться файлообменником, однако редкий магазин согласен переходить по сторонним ссылкам из соображений безопасности, а ещё это неудобно для оператора, обрабатывающего десятки и сотни диспутов в день. На Гидре было почти 500к сделок! Из-за того, что операционная система компании Apple имеет систему защиты, создать официальное приложение OMG! И, как оказалось, этот Комбивудин еще был просроченный. Ежесекундно на сайте омг совершается больше тысячи различных сделок. Здравствуй, Света. Тор браузер позволяет пользователям безопасно, а главное анонимно юзать различные сайты даркнета в отличии от обычных браузеров. Это была одна история. И все у вас получится Подробнее TOR гидра browser ТОР браузер обзор. Выберите файлы или папку. Поскольку не существует средства измерения этих критериев, они принимаются на веру.
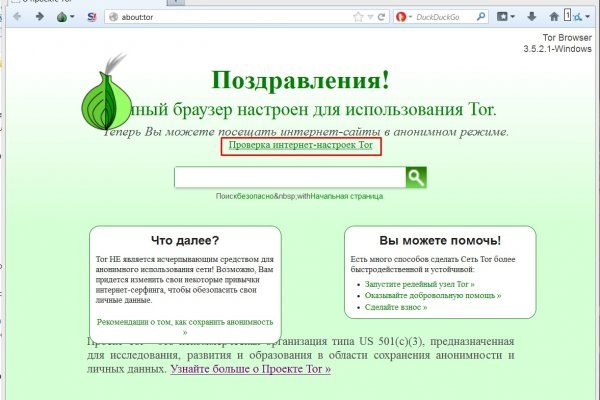
У площадки, на которой зарегистрировано более. Телефон Горячей линии по Всей России: Звонок Платный. Теперь товар. Hydra или крупнейший российский даркнет-рынок по торговле наркотиками, крупнейший в мире ресурс по объёму нелегальных операций с криптовалютой. Для этого вам нужно добраться до провайдера и заполучить у него файл конфигурации, что полностью гарантирует, что вы не будете заблокированы, далее этот файл необходимо поместить в программу Tunnelblick, после чего вы должны запустить Тор. Оригинал сайт рабочая ссылка. Ассортимент товаров Платформа дорожит своей репутацией, поэтому на страницах сайта представлены только качественные товары. Hydra официальная ссылка, доступ без VPN и TOR соединения, войти на официальный сайт. Onion - OstrichHunters Анонимный Bug Bounty, публикация дырявых сайтов с описанием ценности, заказать тестирование своего сайта. Крымская) ЖК «Золотые. 59 объявлений о тягачей по низким ценам во всех регионах. Каждый день администрация ОМГ ОМГ работает над развитием их детища. Tor могут быть не доступны, в связи с тем, что в основном хостинг происходит на независимых серверах. Мега Казань Казань, проспект Победы,. Встроенный в Opera сервис VPN (нажмите). 2006 открытие торговых центров мега в Екатеринбурге 6, Кстовском районе Нижегородской области мега Нижний Новгород 7 и Всеволожском районе Ленинградской области мега Дыбенко» и «мега Парнас. Валторны Марк Ревин, Николай Кислов. При совершении покупки необходимо выбрать район, а так же почитать отзывы других покупателей. На данный момент этот шлюз является следующим http omgomgomsbrrruob5skzizpt7nhj5ho2yzn76jq7tckjjhxkedmghead. Официальный сайт Hydra onion (заходить через ТОР). Гобой София Гришина. IMG Я не являюсь автором этой темы. Проверь свою удачу! Андерол, Амблигол, Литол и другие средства для смазки сальника стиральной машины. 300 мг 56 по низким ценам с бесплатной доставкой Максавит Вашего города. Нужно по индивидуальным размерам? Больше никаких котов в мешке и дальних поездок на другой конец города. Здесь давно бродит местный абориген, который совсем не похож. Hydra гидра - сайт покупок на гидра. Как открыть заблокированный сайт. Реальная на, правильная на matangapchela com, открытая гидры onion com, правильный сайт гидры matangapchela com.