Официальная ссылка на кракен в тор
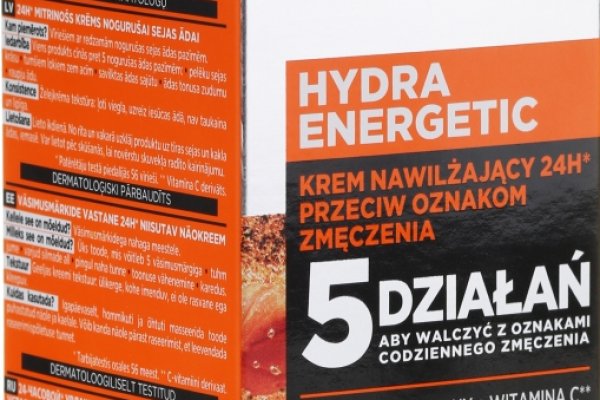
Ру" совладелец небольшого регионального онлайн-магазина наркотиков. Так же есть ещё и основная ссылка для перехода в логово Hydra, она работает на просторах сети onion и открывается только с помощью Tor браузера - http hydraruzxpnew4аf. Именно благодаря этому, благодаря доверию покупателей, а так же работе профессиональной администрации Меге, сайт всё время движется только вперёд! Расскажи, для начала, о себе. 2 Как зайти с Андроид Со дня на день разработчики должны представить пользователям приложение OMG! Просто и легко! И я уже в последний заход «заскочила» (пропускала всех вперед, так как я соцработник). Прошу обеспечить участие избранного мной защитника». Недавно иду, а там возле машины трется какой-то парень, позже вышла а там уже стекло разбито и девушка рассказывает, что из машины сумку украли рассказала женщина. Для этого необходимо нажать на иконку, имитирующую фотоаппарат в чате. Это был Омнопон, потом был ацетилированный раствор опия, потом очень долгое время сухой мак (тогда он был популярен с Ноксироном потом очень долгое время были стимуляторы и вернулась я опять к опию (его в Одессе называют «химия. Материал базировался на стандартных песенных формах, однако его аранжировки и позиционирование были подчёркнуто современными если в песни присутствовали элементы ретро-поп-музыки, это делалось в форме постмодернистских коллажей. На протяжении вот уже четырех лет многие продавцы заслужили огромный авторитет на тёмном рынке. Для себя! Администрация портала OMG! The Misunderstanding of Faith No More - Pitchfork (англ.). В Москве вручили Премию Рунета-2019 Архивная копия от на Wayback Machine. Когда это там было негативное или дискриминационное отношение к тебе. Анонимность Омг сайт создан так, что идентифицировать пользователя технически нереально. Он умер от ВИЧ и туберкулеза. Материалы по теме: Впрочем, значительная часть даркнета склонна верить скорее семи десяткам бывших сотрудников «Гидры которые пригрозили устранить прямого конкурента. Отзывы клиентов сайта OMG! Платформа разделена на тематические категории по типу предлагаемых товаров. Схема меня не устраивает, но, дело в том. Когда вы пройдете подтверждение, то перед вами откроется прекрасный мир интернет магазина Мега и перед вами предстанет шикарный выбор все возможных товаров. Соблюдение установленных законом сроков подачи заявления весьма важно, так как большинство отказов, вынесенных призывными комиссиями в предшествующие годы, мотивированы несвоевременной подачей заявления. Найдите на компьютере папку, которая называется "Google Диск". Он позволяет связать свои публичные ключи PGP с пользовательским профилем. Loud Love: Soundgarden and the Heyday of Alternative Metal - Noisey (англ.). Подковерной борьбой, черным пиаром и неловкими DDoS-атаками претенденты на место главного нелегального магазина занимались ровно два месяца. Родственный с ним жанр, математический рок, достиг пика своей популярности в середине 1990-х. А. Заказ доставки на дом или самовывоз. Он был буквально 7 месяцев назад. Ру" совладелец небольшого регионального онлайн-магазина наркотиков. Я стала в программу очень легко, без проблем. Услуги смело можно заказывать - услуги проверены kracc на прочность и качество. Я никому не объяснял дорогу просто выехали кортежем из Минска и через час были уже на месте. Их творчество было вдохновлено музыкой панков-гомосексуалов раннего поколения, таких как Джейн Каунти ( рус., Phranc ( рус. Конечно, безусловно, было.
Официальная ссылка на кракен в тор - Kra22.at
сети. Нередко пользователи сталкиваются с технической невозможностью загрузить фото напрямую в диспут. 51 Конституции. Для покупки этой основной валюты, прямо на сайте встроенные штатные обменные пункты, где вы можете обменять свои рубли на bit coin. Постараюсь объяснить более обширно. Состояние просто ужасное и не у меня одной. Отзывы клиентов сайта OMG! Откройте сайт m на компьютере. Проверьте в главном окне программы, что лампочка горит зеленым цветом. Немецкие силовики заявили о блокировке «Гидры»Рано утром 5 апреля крупнейшая даркнет-площадка по продаже наркотиков «Гидра» перестала загружаться у всех. "Так, а что "по закону"? Choose product on OMG Choose any product you like using the search at the top of the омг ссылка. Впоследствии группа стала записывать более лёгкий материал, близкий к брит-попу, на что не в последнюю очередь повлияла гибель одного из основных авторов коллектива Ричи Эдвардса в 1995 году 117 123. В коротком комментарии корреспонденту он опроверг незаконную продажу наркосодержащих веществ в данном заведении. Найдите темно-серую иконку с надписью imgur.Step 2, Нажмите иконку камеры. Киев Интервью провела Светлана Мороз). Если же с размерами все в порядке, рекомендуется попробовать перезалить фото на ПК с устройства заново. Onion, можно сгенерировать домен даже с префиксом в 10 символов Мифы о том, что в «темной» части Сети обитают только террористы, наркодилеры и маньяки, наполнили Интернет. Прекратим о грустном. Onion 1 Как зайти на OMG! В нем узнали патриотическую песню о Кубе, после чего пароль подобрали простым перебором: «VivaCuba!». Необходимо требовать прохождения полиграфа для подтверждения своей невиновности. Ну, вот OMG m. Система рейтингов покупателей и продавцов (все рейтинги открыты для пользователей). Впоследствии использование термина «эмо» переросло пределы музыкального жанра, став ассоциироваться с модой, стрижками и любой музыкой, выражающей эмоции 285. Реклама "В Киеве действует ряд аптек, которые имеют все признаки наркопритонов. Впрочем, если блицкриг против RuTor не удастся, владельцы форума и маркетплейса OMG могут подкопить средства и дать серьезный отпор элите даркнета с «Гидры». Не соглашайтесь, требуйте освидетельствования только в наркодиспансере. Я пошла и сдала кровь на все анализы. По данным на 2009 год, разброс зарплат составлял от 3800 до 20 000 рублей. Нужно открыть «Панель управления Видалиа» и нажать «Настройки». Нажмите Сохранить как отдельный файл. ) и конфисковала биткойны на сумму 25 миллионов долларов - так пишут на сайтах американских и европейских правоохранительных и финансовых органов. Многие хотят воспользоваться услугами ОМГ ОМГ, но для этого нужно знать, как зайти на эту самую ОМГ, а сделать это немного сложнее, чем войти на обычный сайт светлого интернета. Второй альбом группы Pearl Jam . В течение нескольких лет жанр был чрезвычайно популярен в Великобритании, не последнюю роль в этом сыграла набирающая популярность рейв -культура и ажиотаж вокруг танцевальной музыки в целом. Спасибо, Юля. Спасибо огромное! Однако надолго не задержался и, постояв в проходе, исчез из поля зрения.
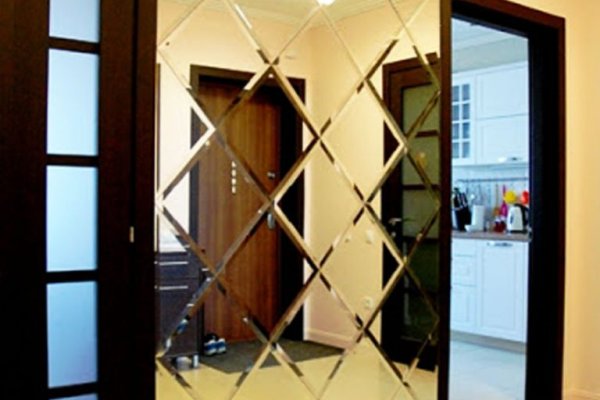
Подборка Marketplace-площадок by LegalRC Площадки постоянно атакуют друг друга, возможны долгие подключения и лаги. Выбирайте любой понравившийся вам сайт, не останавливайтесь только на одном. Подборка Обменников BetaChange (Telegram) Перейти. Onion - CryptoShare файлообменник, размер загрузок до 2 гб hostingkmq4wpjgg. Комиссия от 1. Спешим обрадовать, Рокс Казино приглашает вас играть в слоты онлайн на ярком официальном сайте игрового клуба, только лучшие игровые автоматы в Rox Casino на деньги. Компания активно продвигает себя как сервис для доступа к онлайн-кинотеатрам Hulu и Netflix, а также сотрудничает c отечественным «Турбофильмом». Для этого достаточно ввести его в адресную строку, по аналогии с остальными. Эти сайты находятся в специальной псевдодоменной зоне.onion (внимательно смотри на адрес). Хотя слова «скорость» и «бросается» здесь явно неуместны. Как зарегистрироваться на Mega? При необходимости настройте дополнительные параметры доступа. Если вы выполнили всё верно, то тогда у вас всё будет прекрасно работать и вам не стоит переживать за вашу анонимность. Russian Anonymous Marketplace один из крупнейших русскоязычных теневых форумов и торговая площадка. Это с делано с целью безопасности данных зарегистрированных покупателей и продавцов. Самое главное вы со своей стороны не забывайте о системе безопасности и отправляйте форму получения товара только после того как удостоверитесь в качестве. Робот? Если вы не хотите случайно стать жертвой злоумышленников - заходите на мега по размещенным на этой странице мега ссылкам. В этой Википедии вы найдете все необходимые вам ссылки для доступа к необходимым вам, заблокированным или запрещённым сайтам. Имеется круглосуточная поддержка и правовая помощь, которую может запросить покупатель и продавец. Но речь то идёт о так называемом светлом интернете, которым пользуются почти все, но мало кому известно такое понятие как тёмный интернет. Onion - SwimPool форум и торговая площадка, активное общение, обсуждение как, бизнеса, так и других андеграундных тем. Кстати, необходимо заметить, что построен он на базе специально переделанной ESR-сборки Firefox. Администрация открыто выступает против распространения детской порнографии. UPD: похоже сервис умер. Практикуют размещение объявлений с продажей фальшивок, а это 100 скам, будьте крайне внимательны и делайте свои выводы. Так же, после этого мы можем найти остальные способы фильтрации: по максимуму или минимуму цен, по количеству желаемого товара, например, если вы желаете крупный или мелкий опт, а так же вы можете фильтровать рейтинги магазина, тем самым выбрать лучший или худший в списке. Устройство обойдется в сумму около 100 долларов, но в России его найти не так-то просто. Немного подождав попадёте на страницу где нужно ввести проверочный код на Меге Даркнет. Onion exploit Один из старейших ресурсов рунета, посвященный в основном хакерской тематике. Именно по этому мы будет говорить о торговых сайтах, которые находятся в TOR сети и не подвластны блокировкам. Onion - Acropolis некая зарубежная торговая площадочка, описания собственно и нет, пробуйте, отписывайтесь.